I freelanced at an off-grid solar machine shop in Richmond, Virginia called SolarMill. While at SolarMill I developed graphic design elements to aid in future crowdfunding campaigns, designed, produced, and manufactured off grid routed, laser cut, solar pewter cast, and 3d printed products.
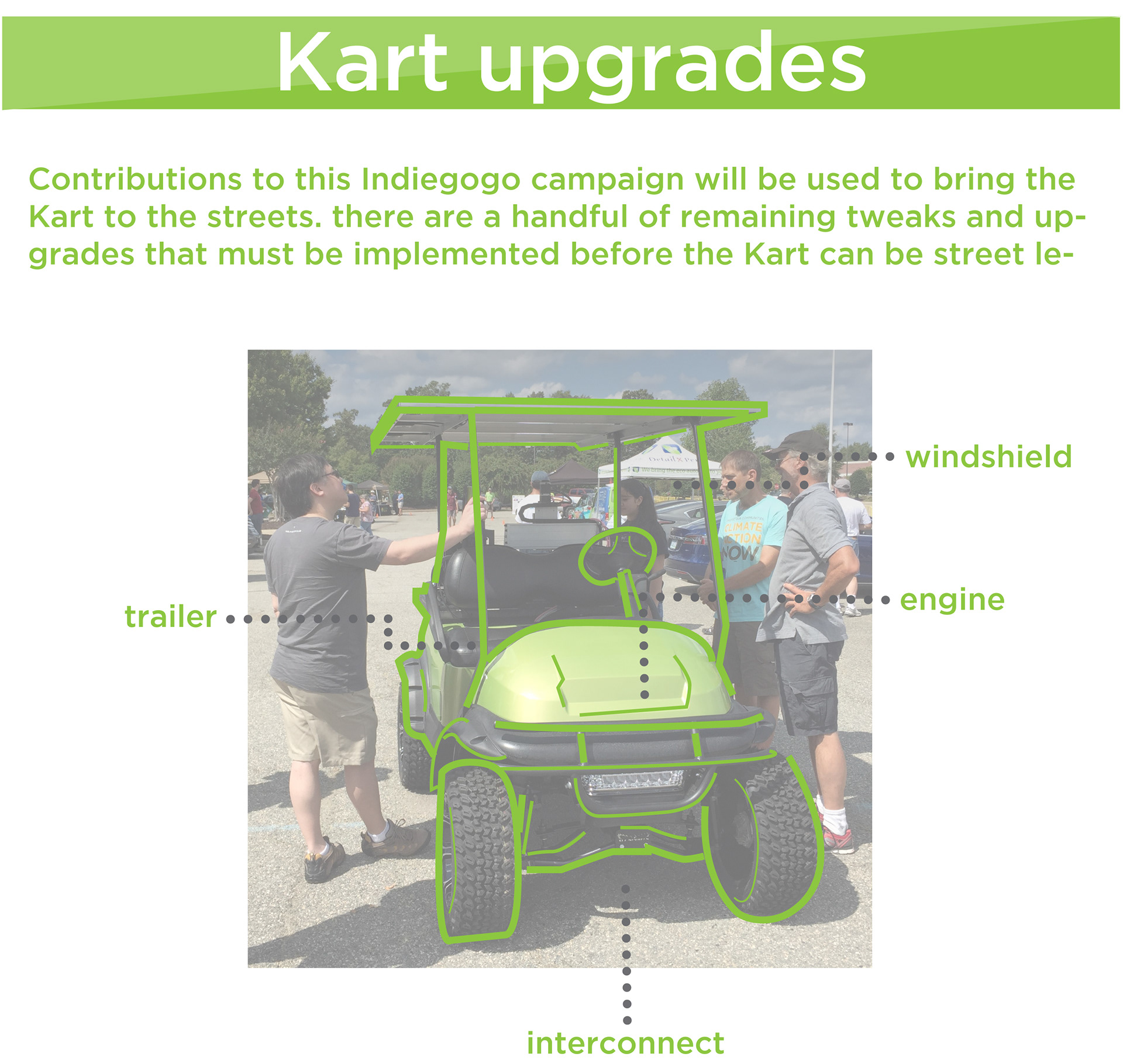

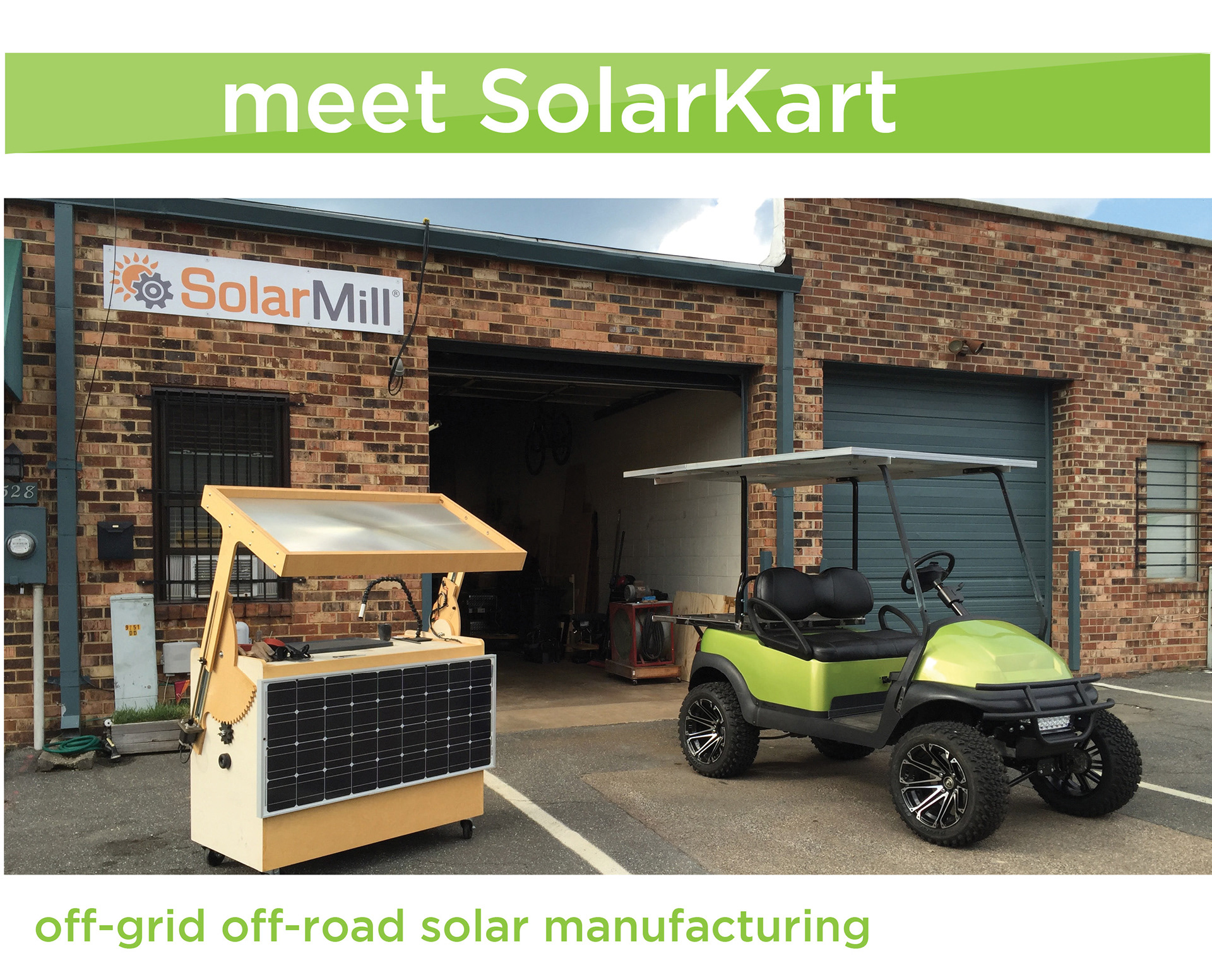
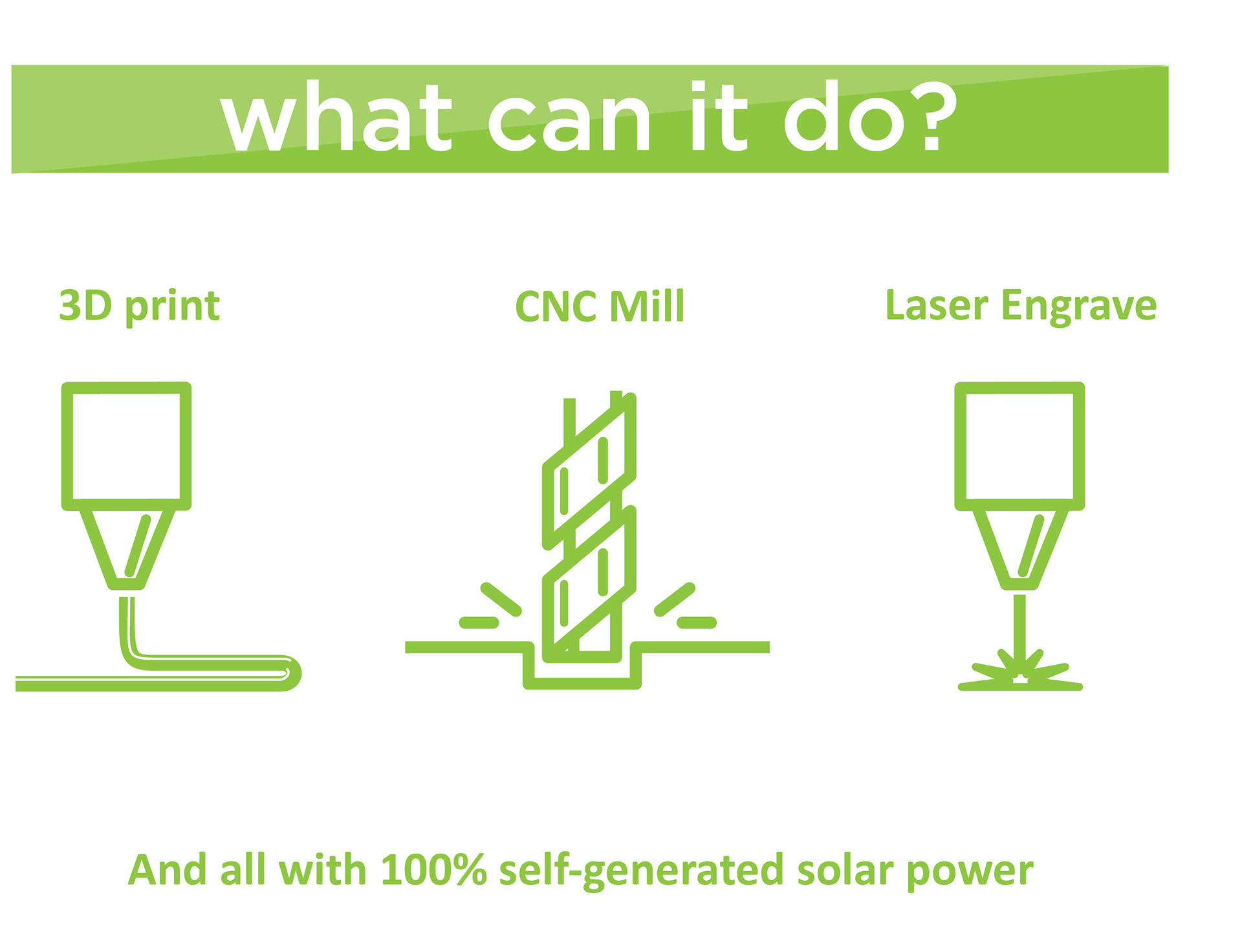
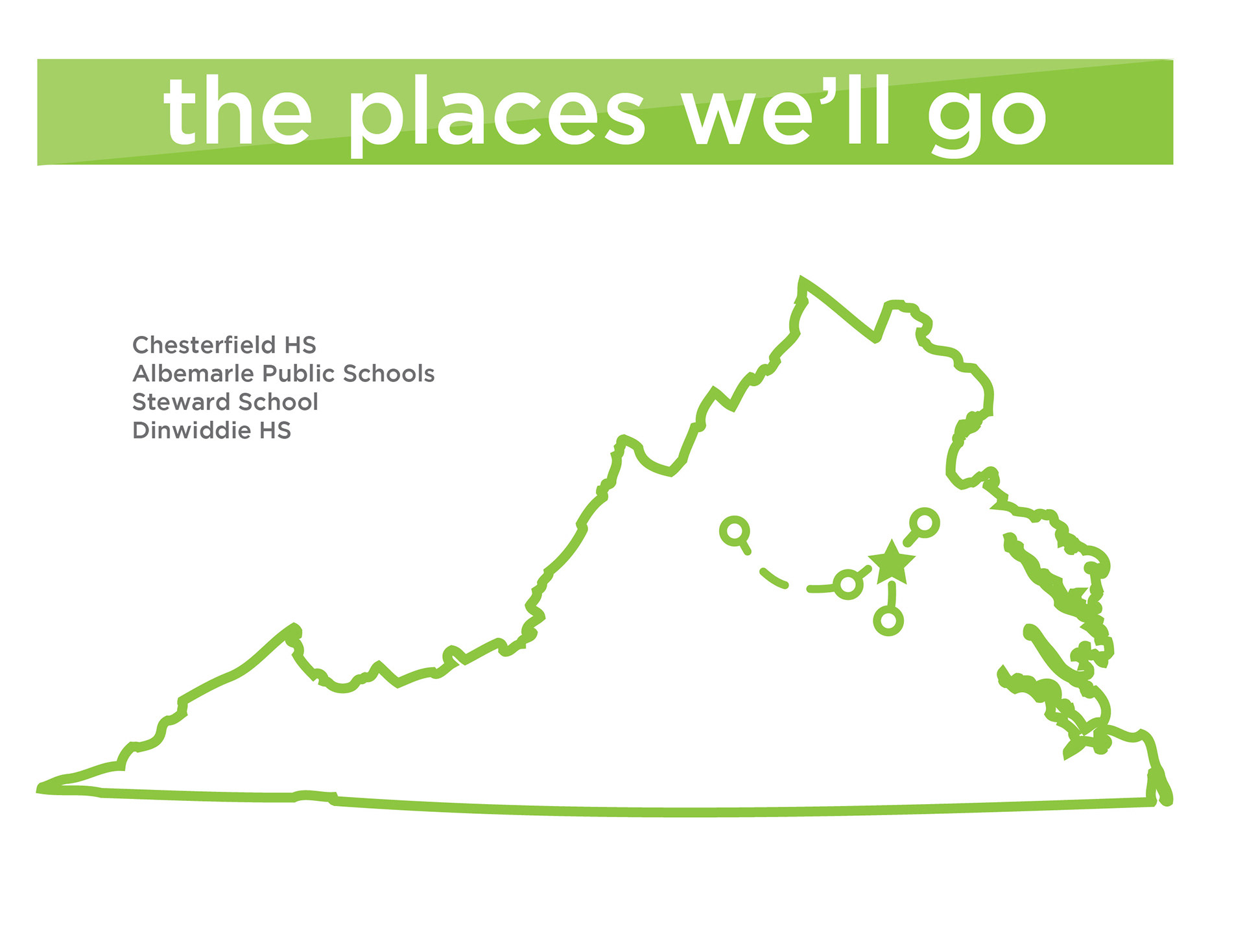

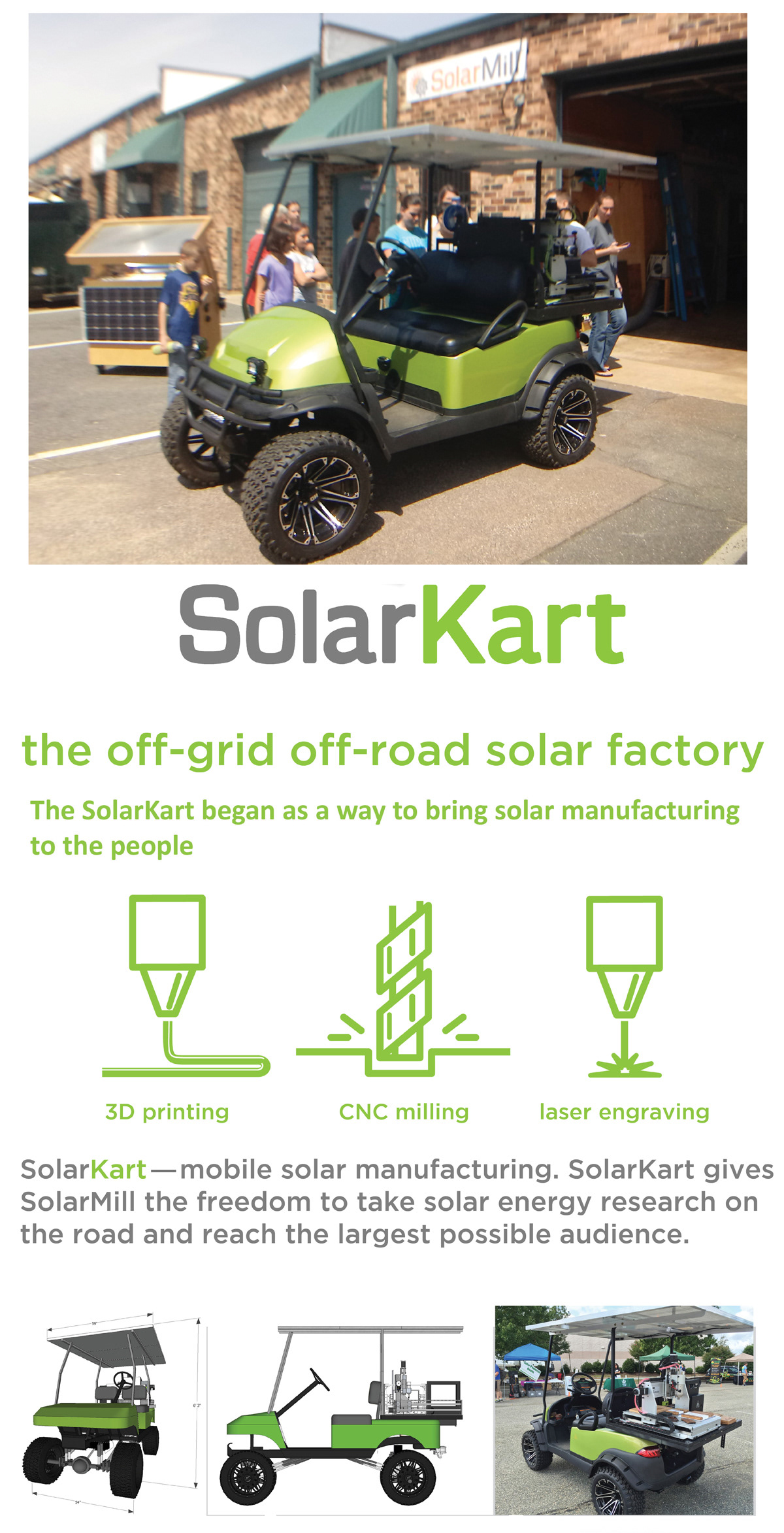
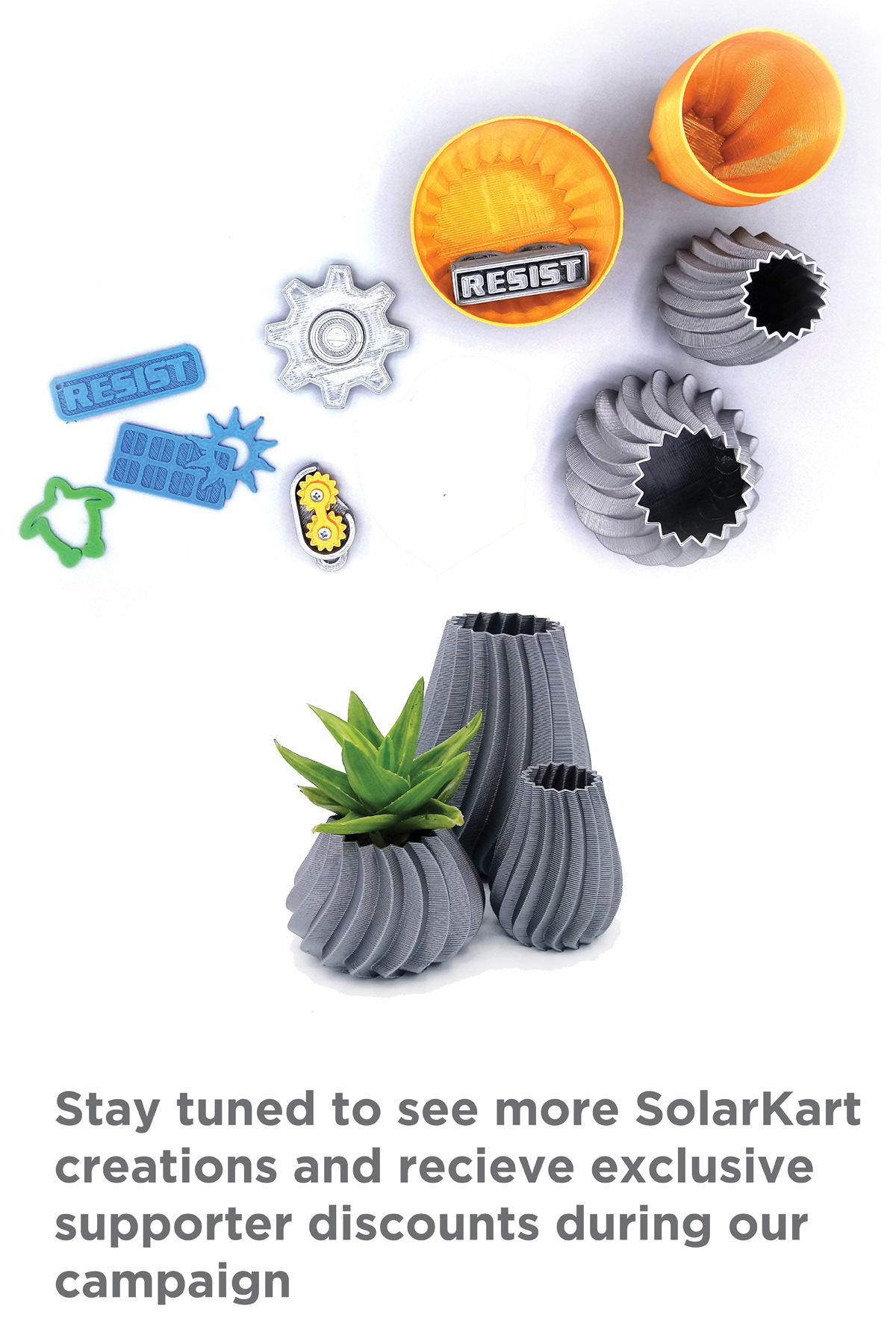
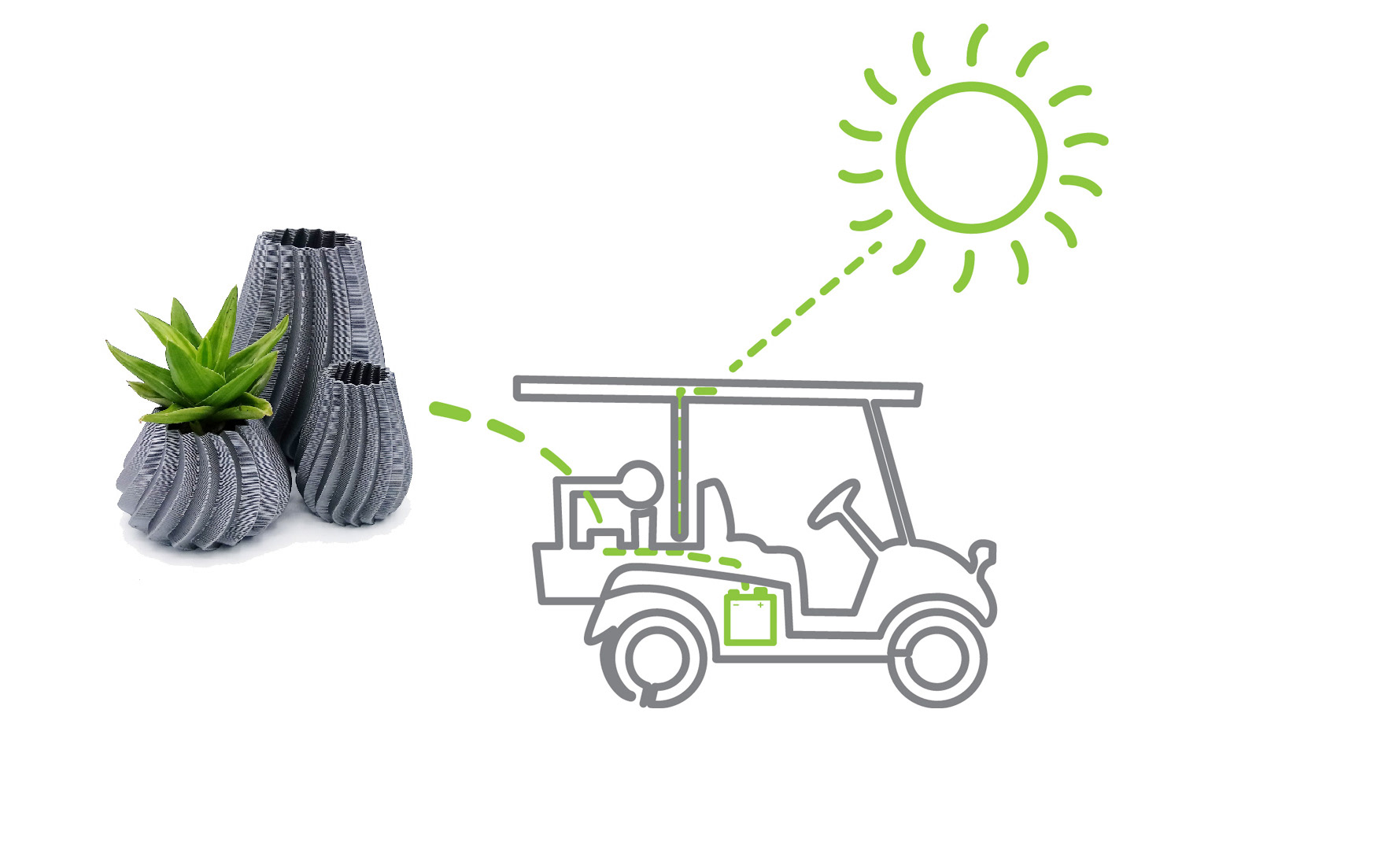
One of my jobs at solar mill was to design and produce energy efficient 3D printed products. By using energy as a constraint I was forced to learn and research deeply into 3d printing and with the added constraint of keeping post processing minimal.
What we found through this exercise was that like all manufacturing processes, 3D printing does some things well, and other things poorly. these would become our design constraints and it meant that we would design for the process-- just like an Industrial designer must design for injection molding, routing, etc. When 3d printing like a product designer and not using it as a form protoyping machine we found that 3d printing has its own unique process constraints and could stand on its own as a manufacturing process when used appropriately.
SolarMill developed a plugin "JoulesCAM" for popular 3dPrinting slicer program "Cura" which displayed estimated power usage in addition to estimated time and material usage. This allowed me to design and iterate 3D models and see their relative energy usage without printing them
What we found through this exercise was that like all manufacturing processes, 3D printing does some things well, and other things poorly. these would become our design constraints and it meant that we would design for the process-- just like an Industrial designer must design for injection molding, routing, etc. When 3d printing like a product designer and not using it as a form protoyping machine we found that 3d printing has its own unique process constraints and could stand on its own as a manufacturing process when used appropriately.
SolarMill developed a plugin "JoulesCAM" for popular 3dPrinting slicer program "Cura" which displayed estimated power usage in addition to estimated time and material usage. This allowed me to design and iterate 3D models and see their relative energy usage without printing them
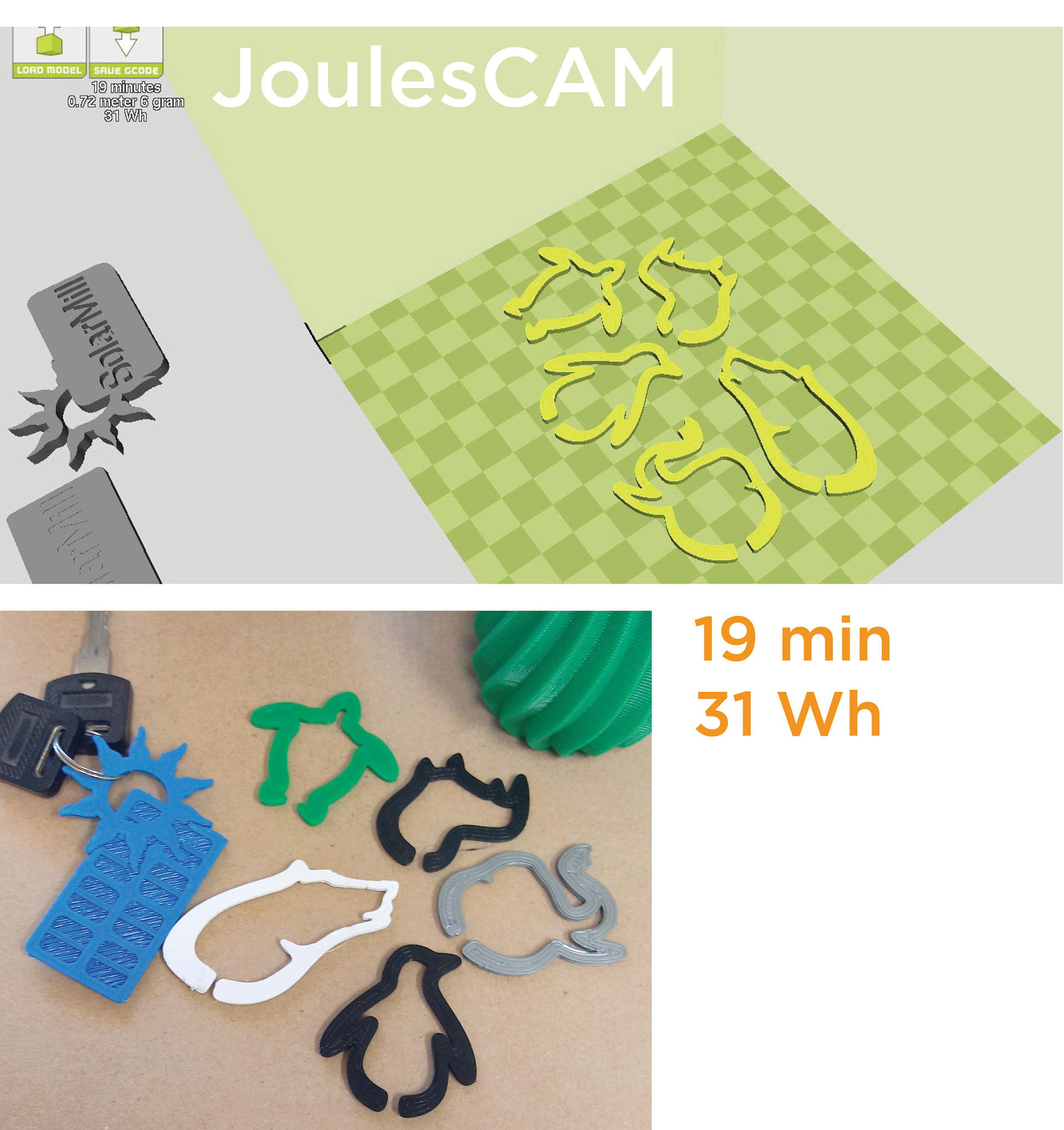
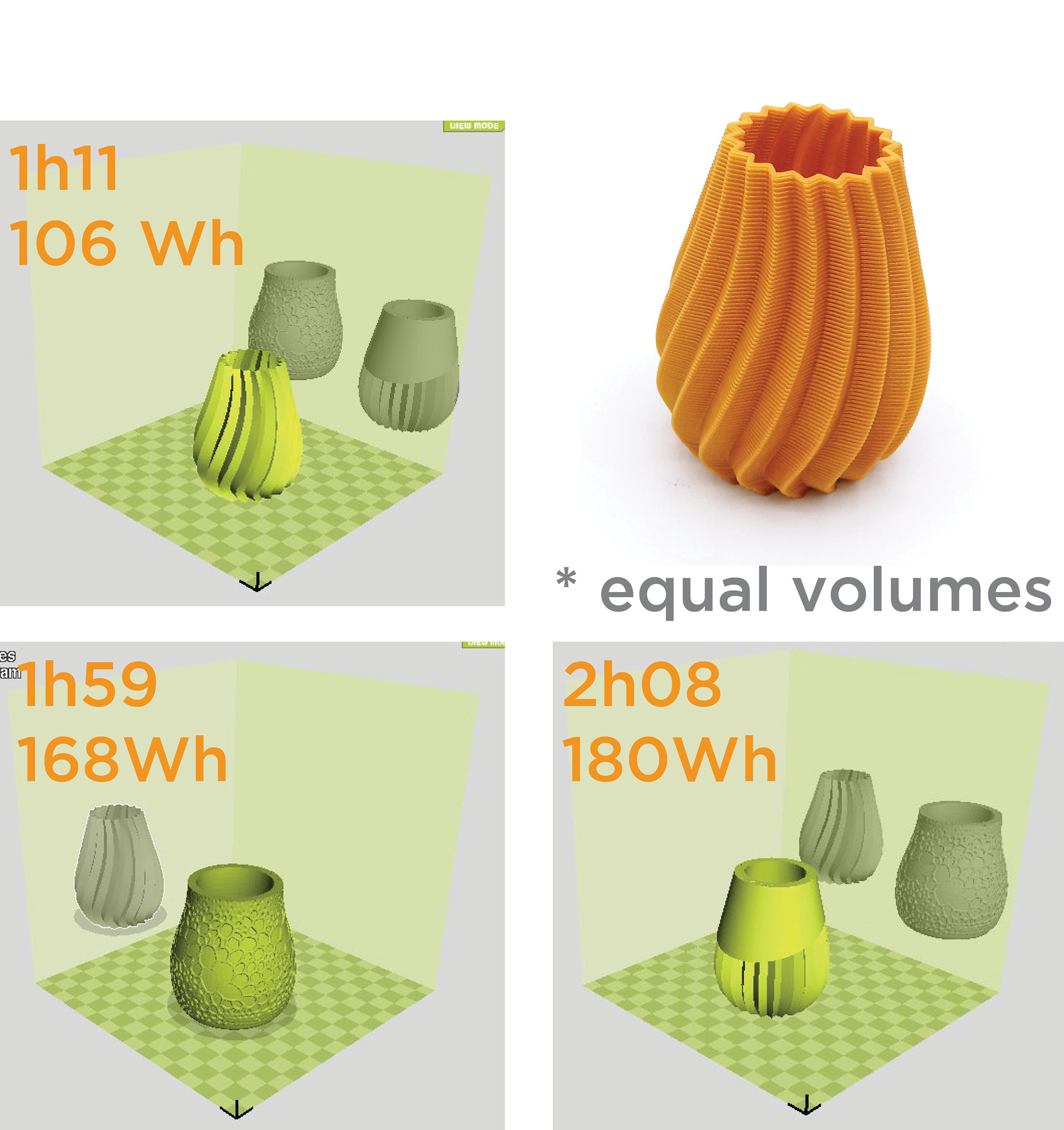
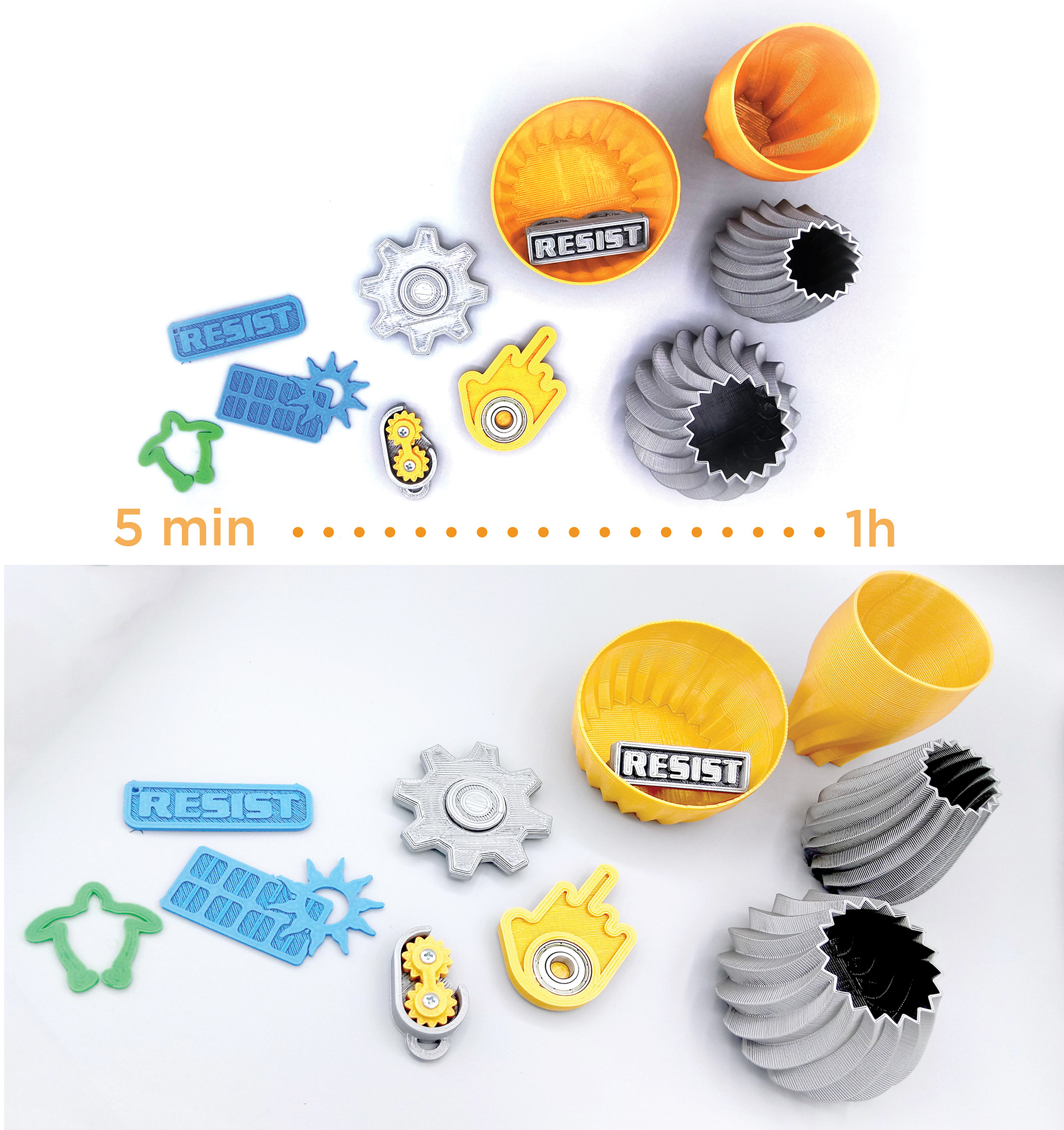
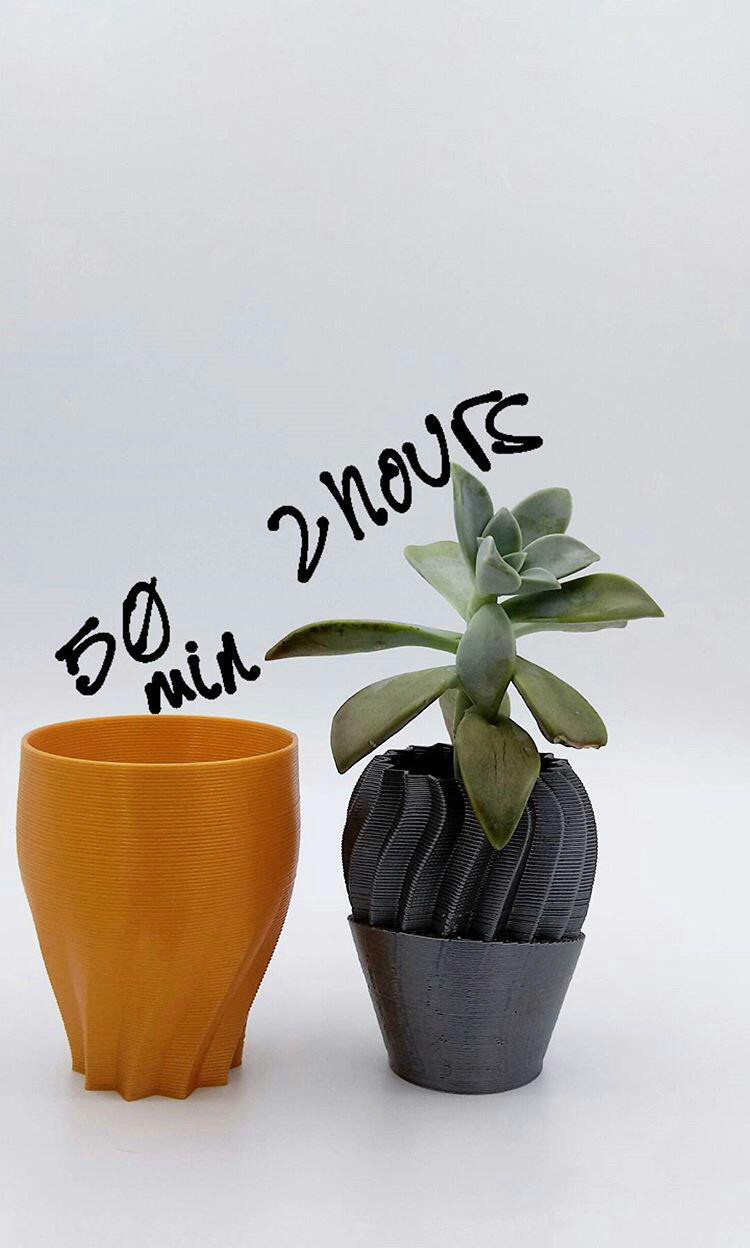
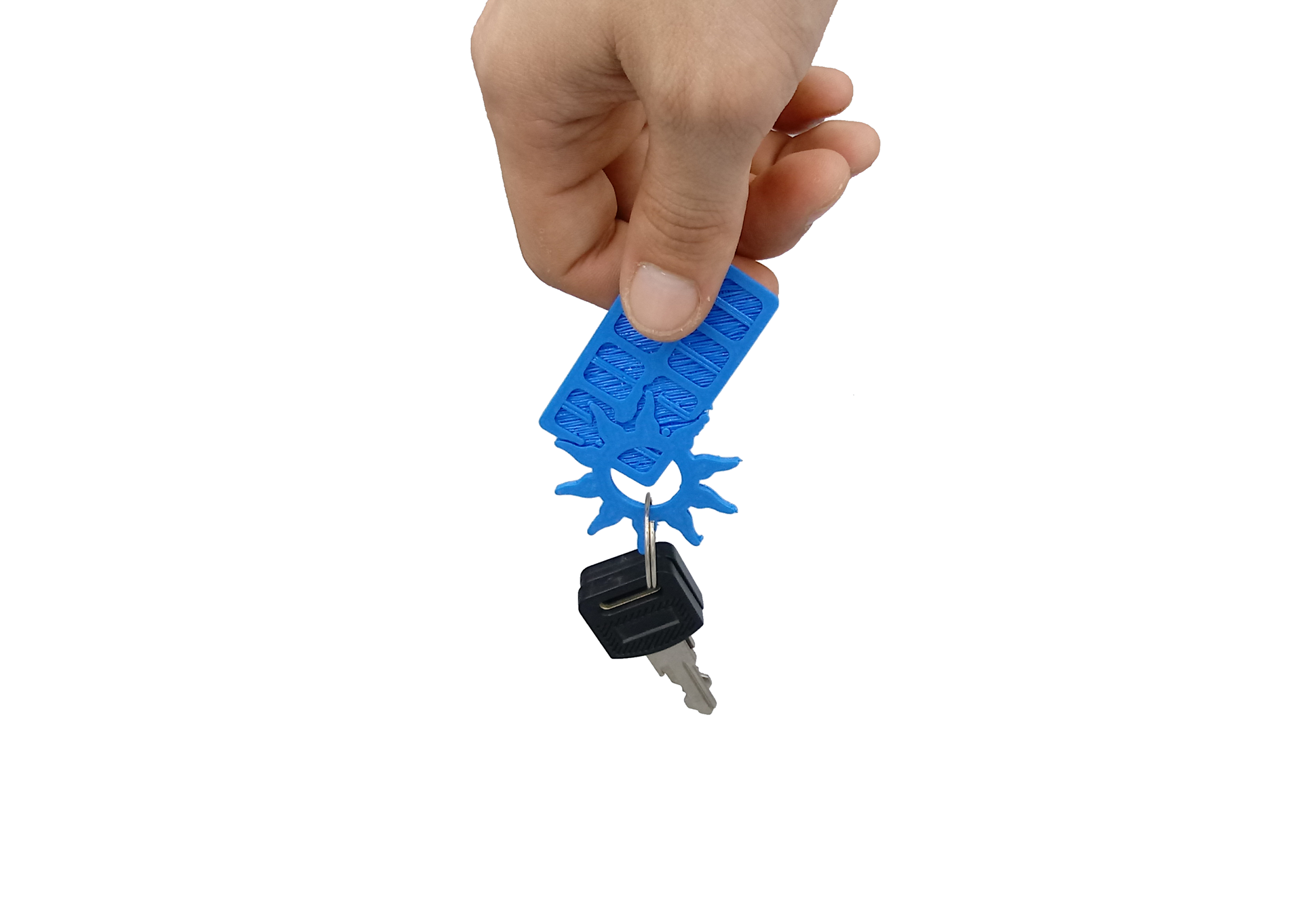
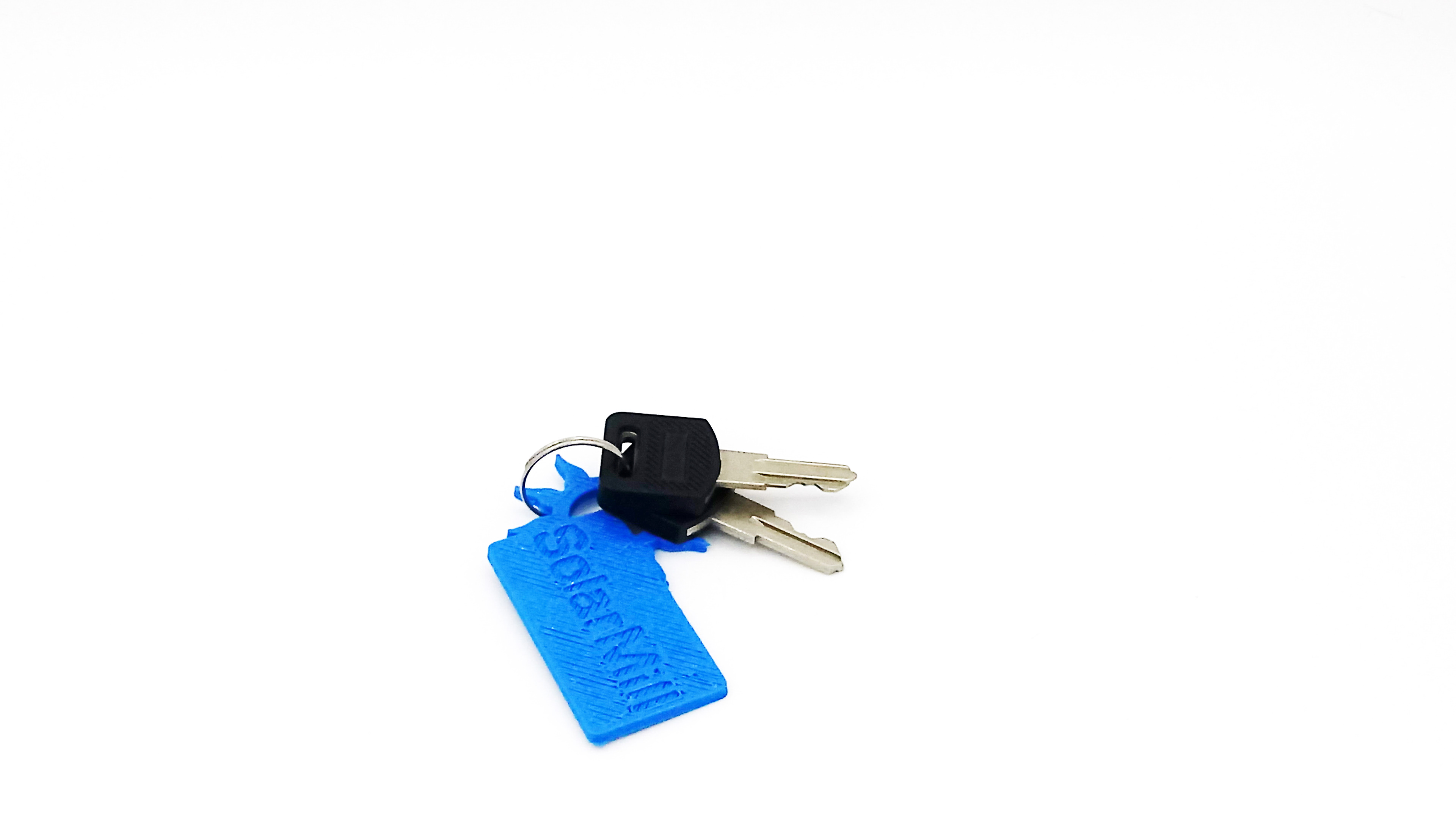
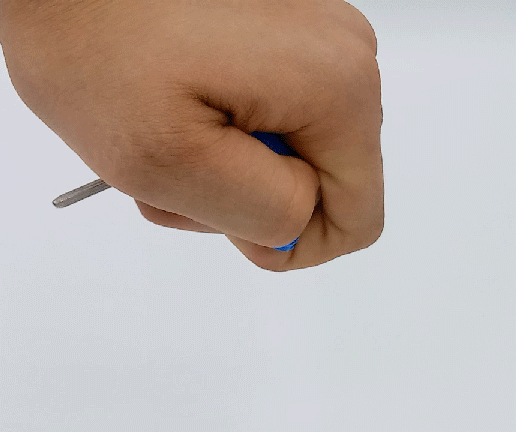
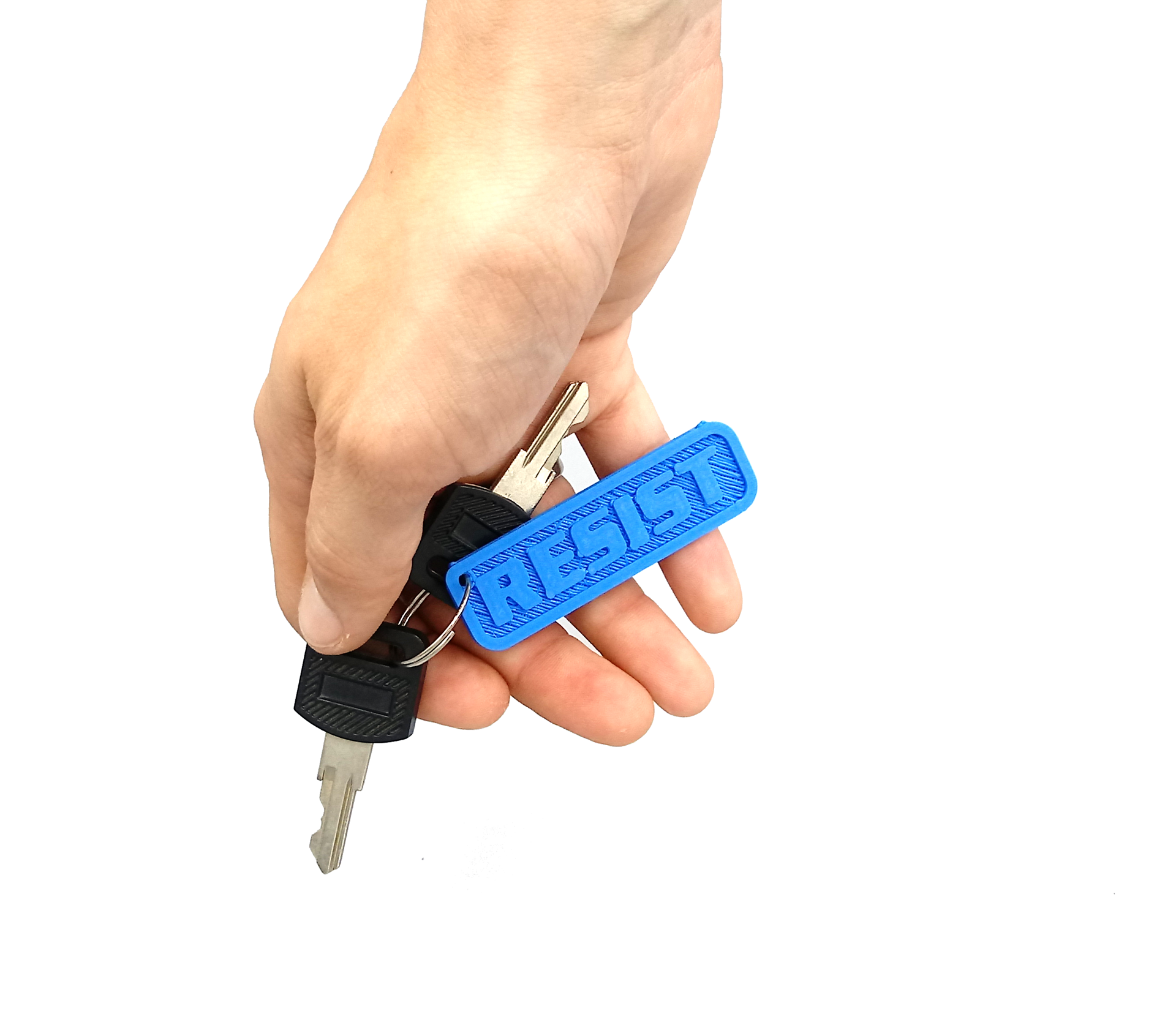
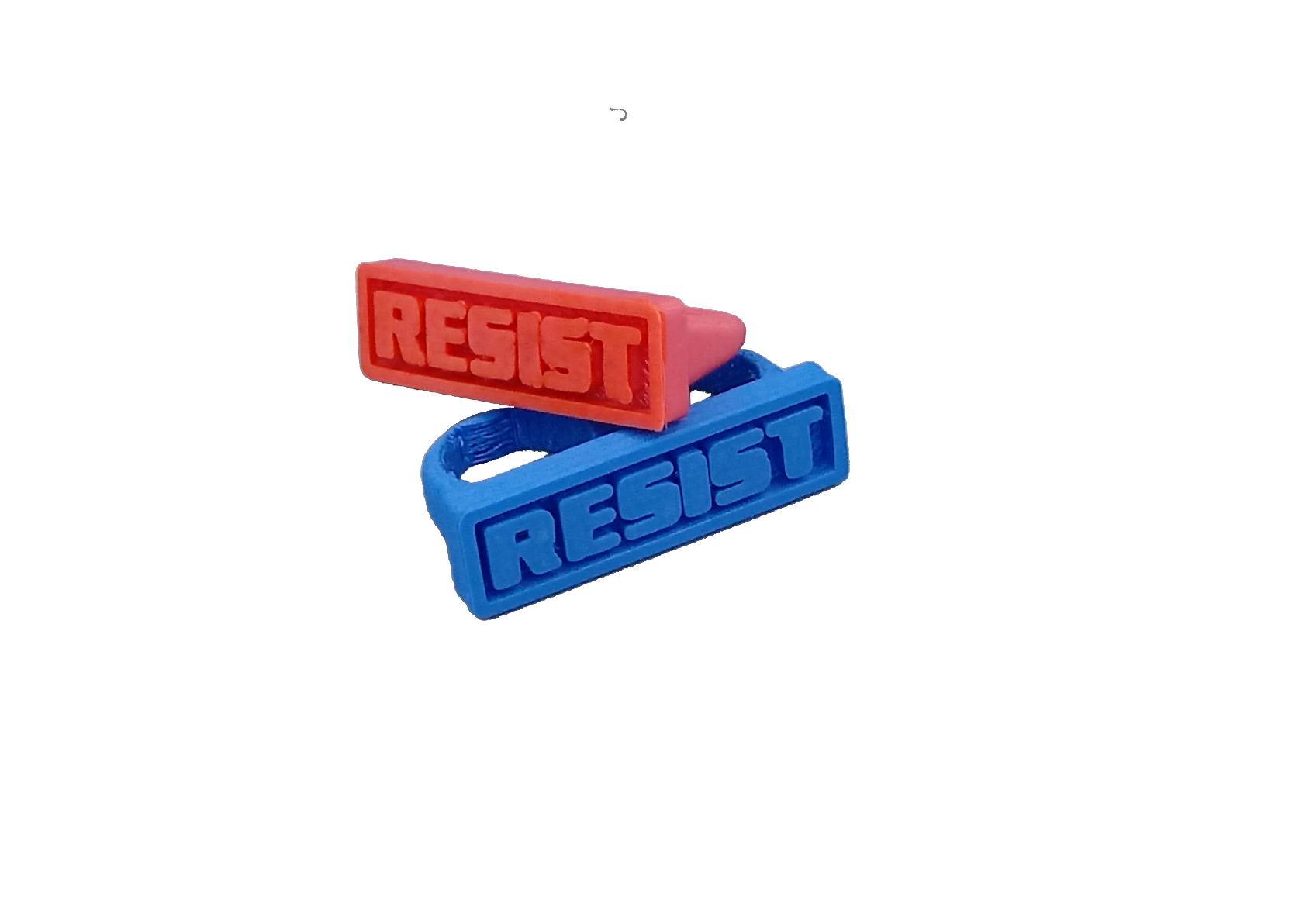
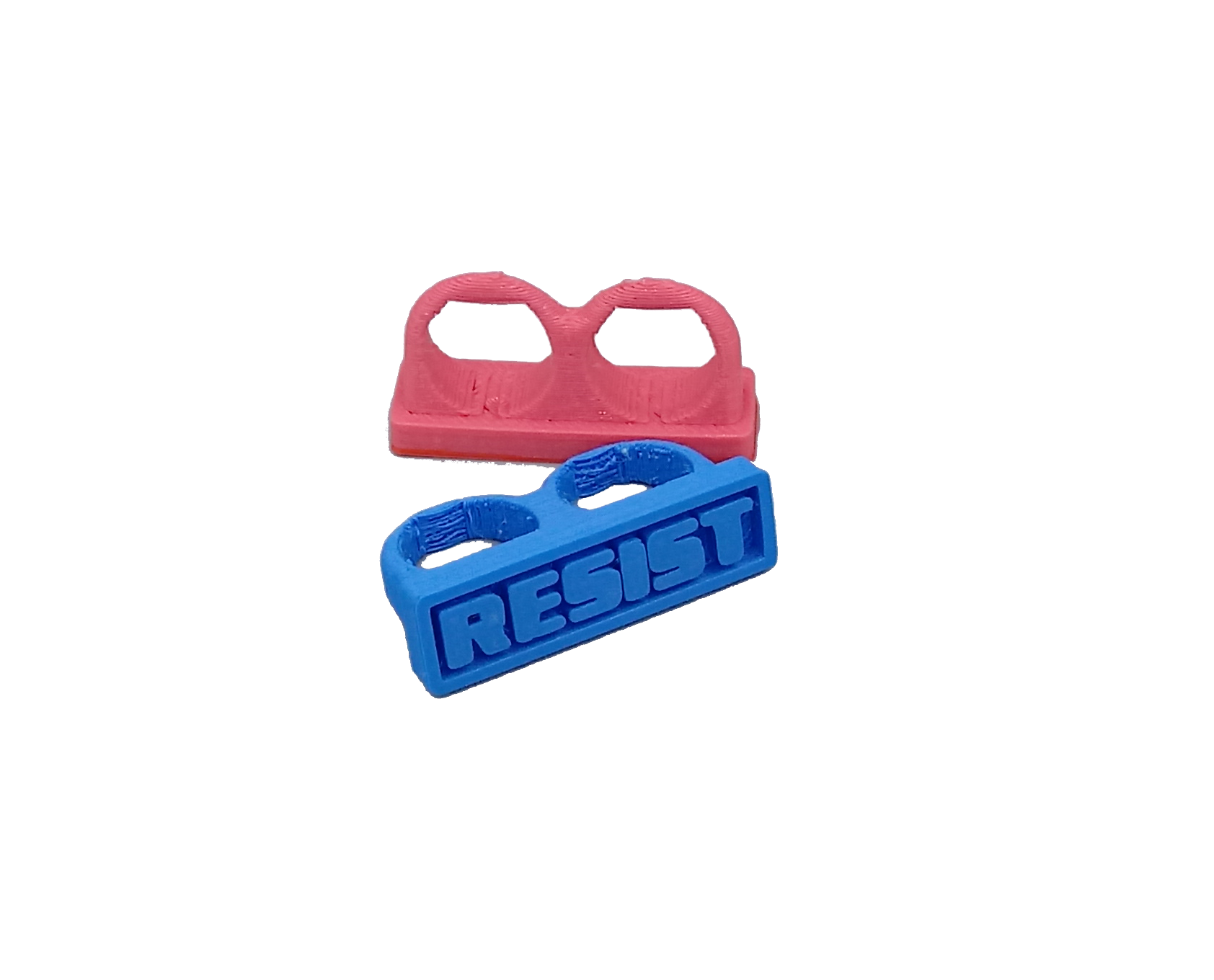
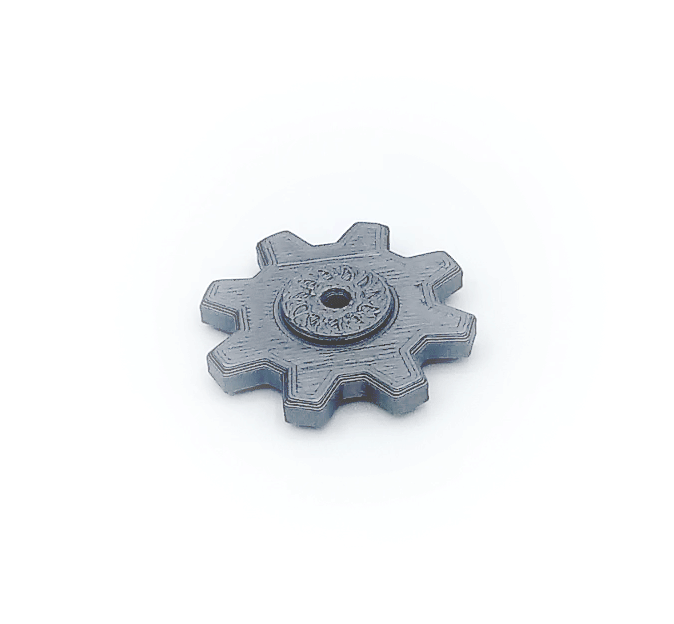
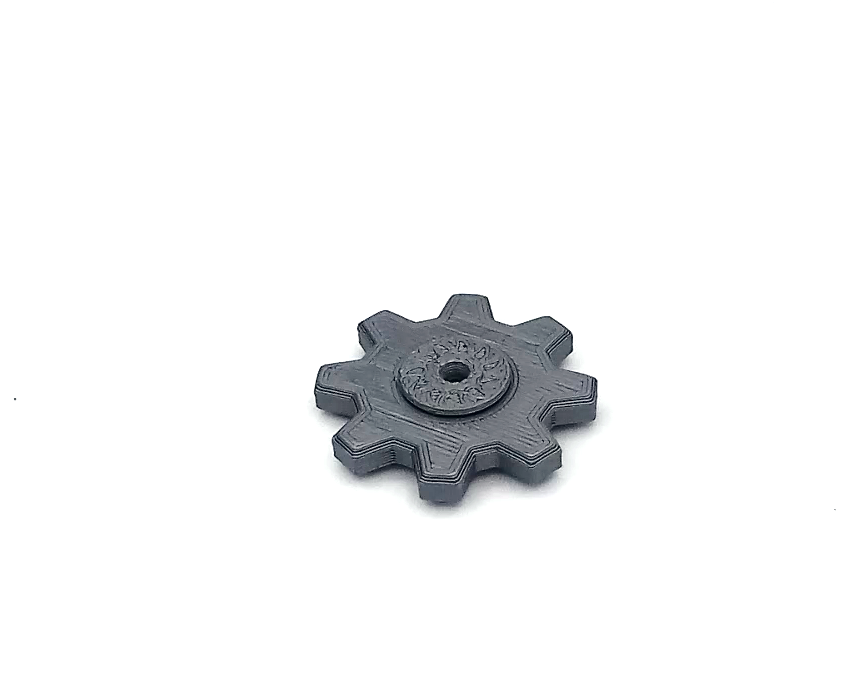
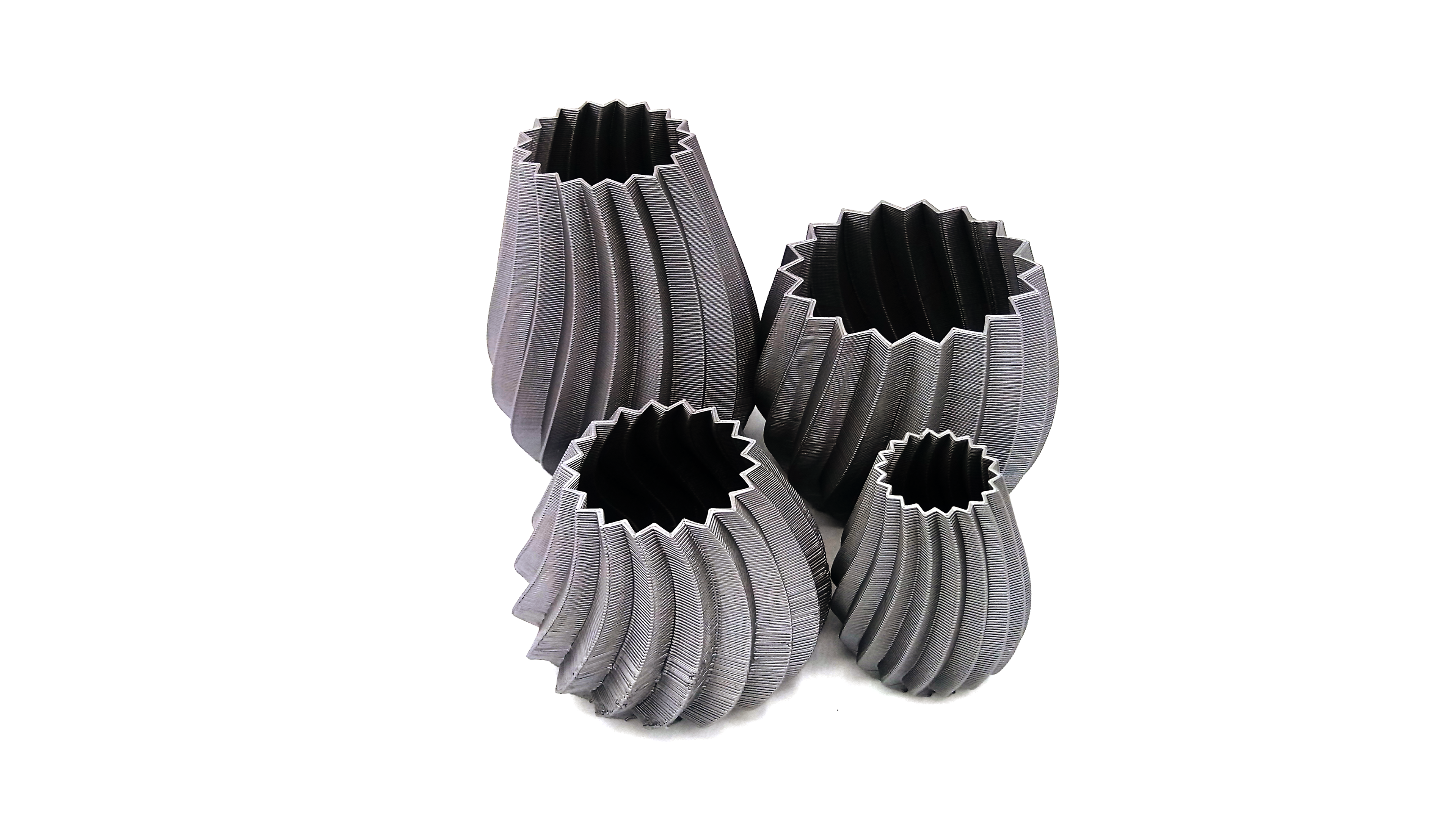
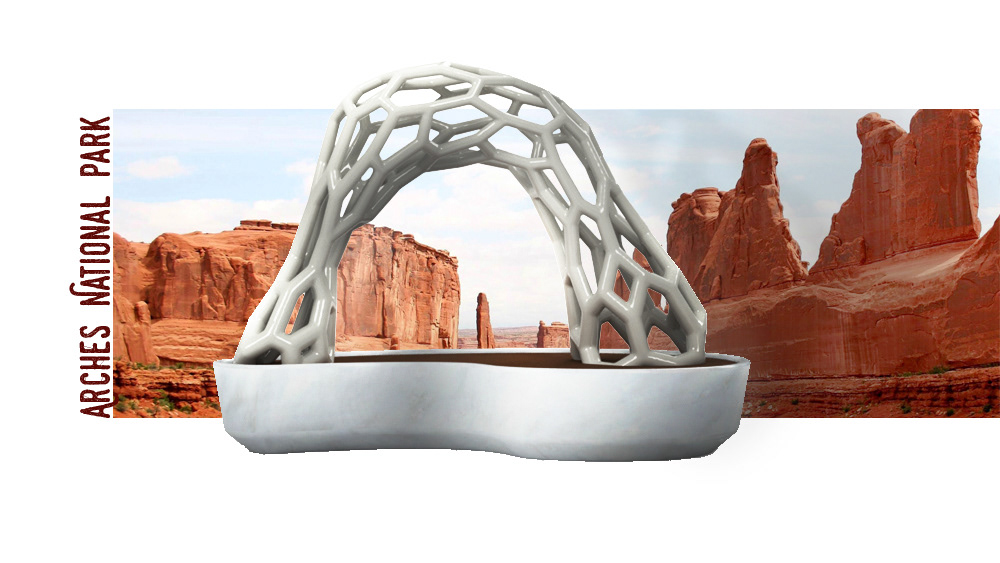
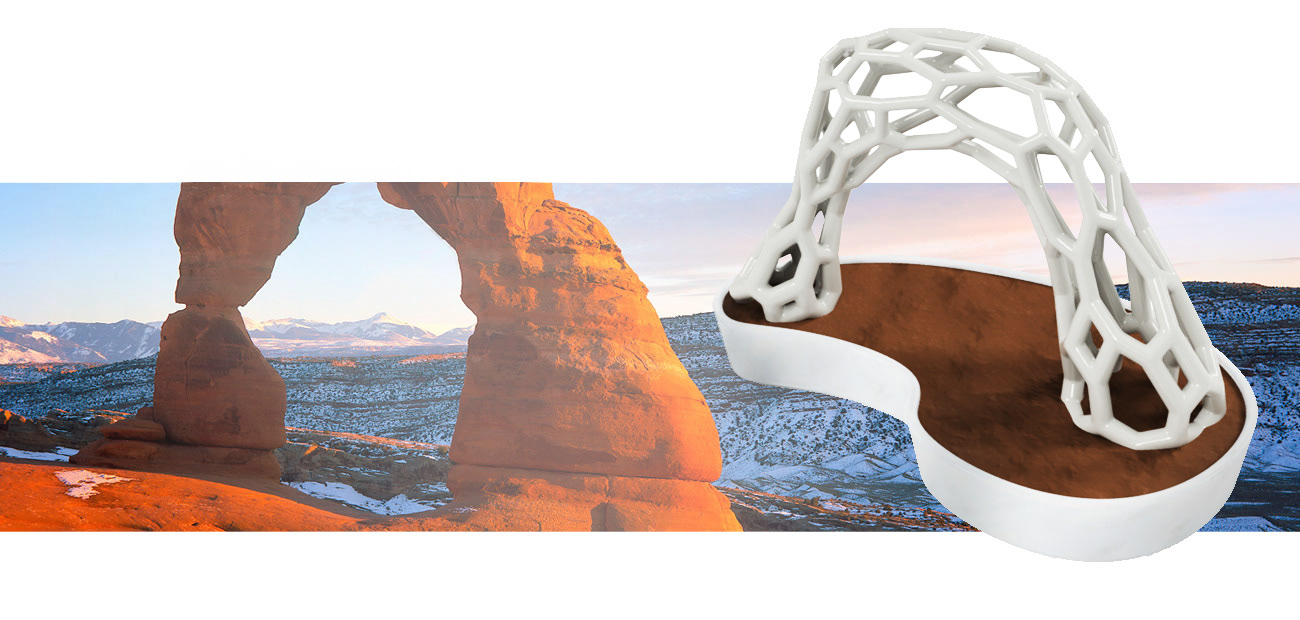
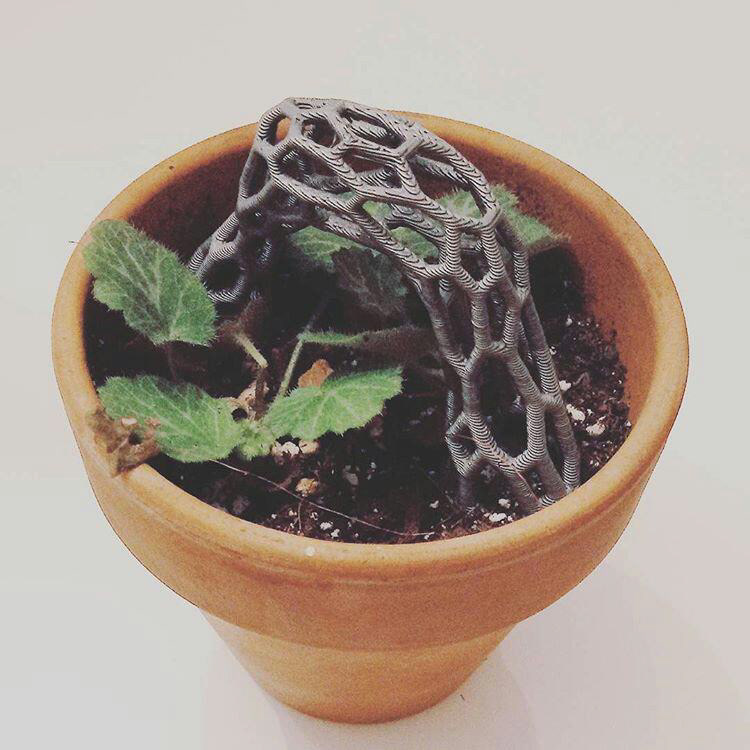
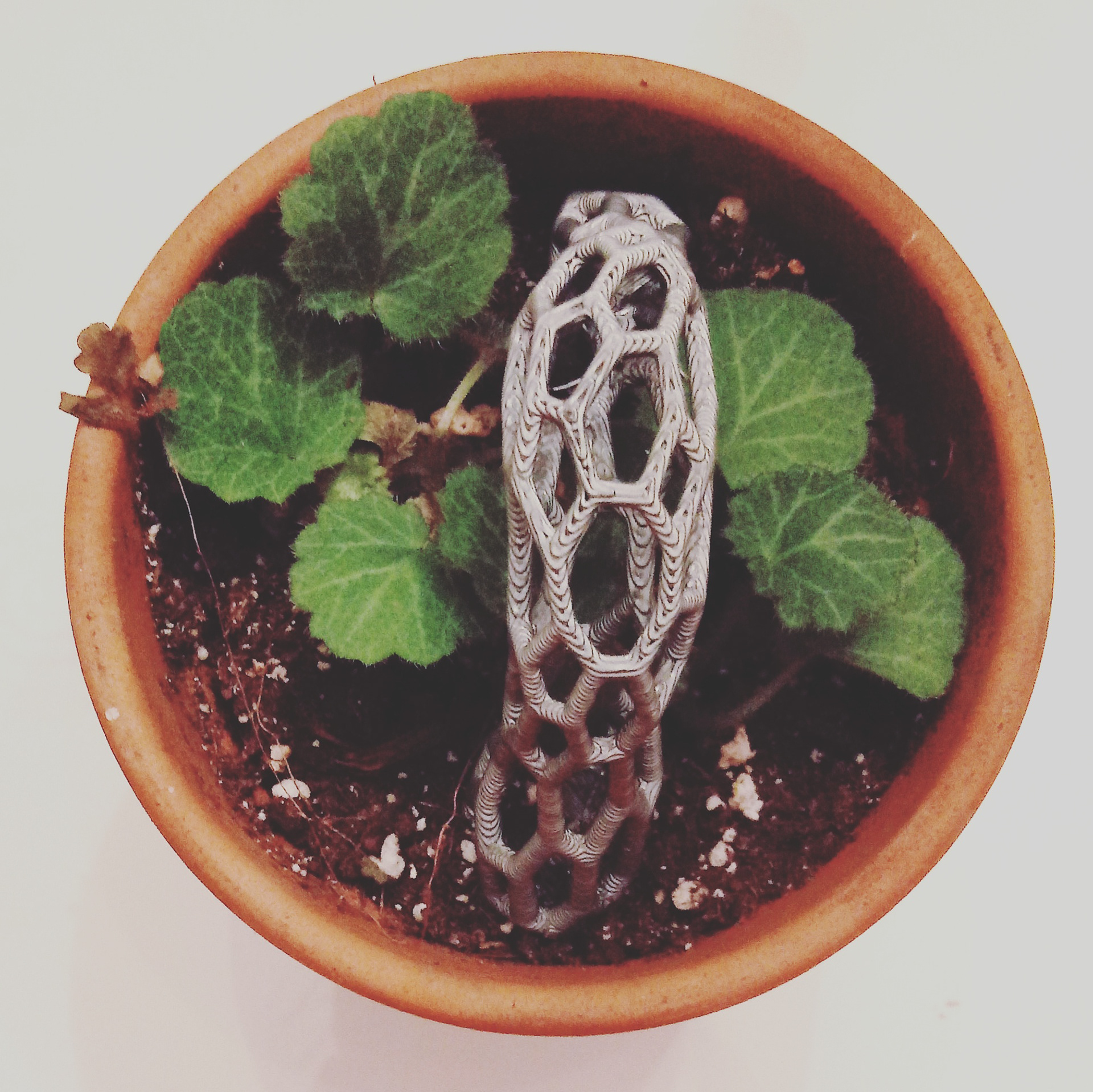
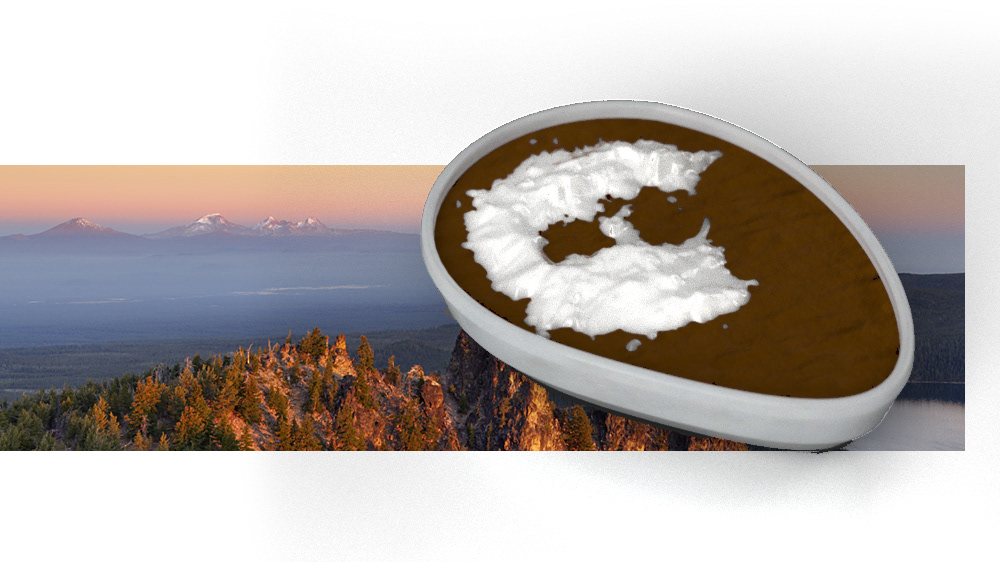
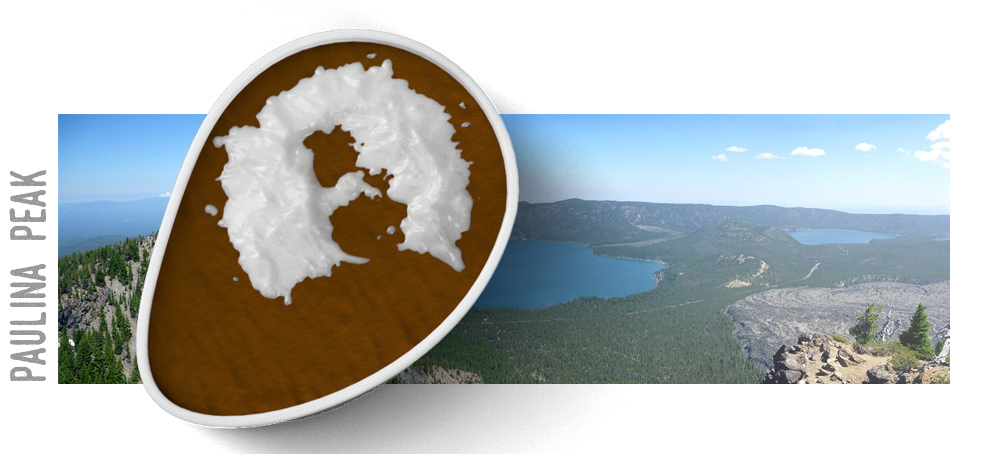
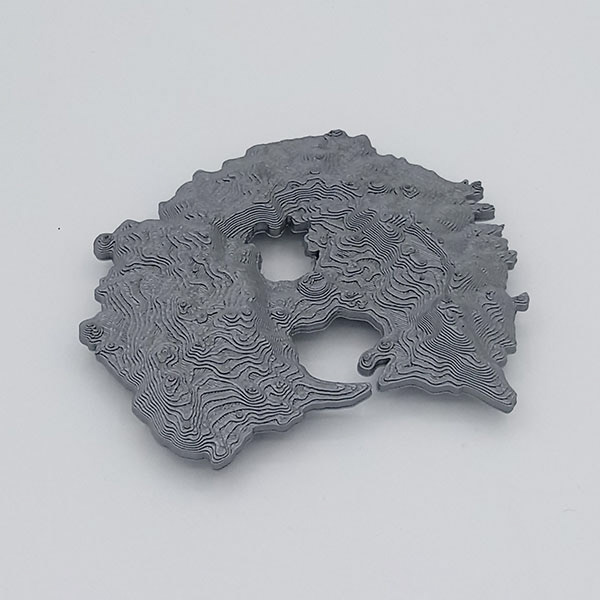
Not only are products developed at Solarmill -- most of the machinery is built from the ground up because there aren't turn-key off grid solutions on the market and to make machinery compatible wih off-grid systems takes a lot of DIY and intuitive designing. While working at SolarMill I helped in the development of a 3d printer - turned 3d engraver o be mounted on the SolarKart. I used fusion 360 to design an enclosure to be lasercut produced, and an air ventilation system that was composed of a low energy bilge pump fan, and a 3d printed part of my own design.
In addition to 3d printing, at Solarmill we had the capability to route, laser cut, and laser engrave products using 100% off-grid solar energy. While freelancing at SolarMill, I designed energy efficient vector illustrations to engrave on solar routed cutting boards. This meant I had to think in terms of tool paths, and use energy as a constraint when designing. With laser engraving and most CAM processes, time= energy. Therefore, using energy or time as a constraint is a way to optimize designs that is relevant to any manufacturer making it a valuable design exercise.
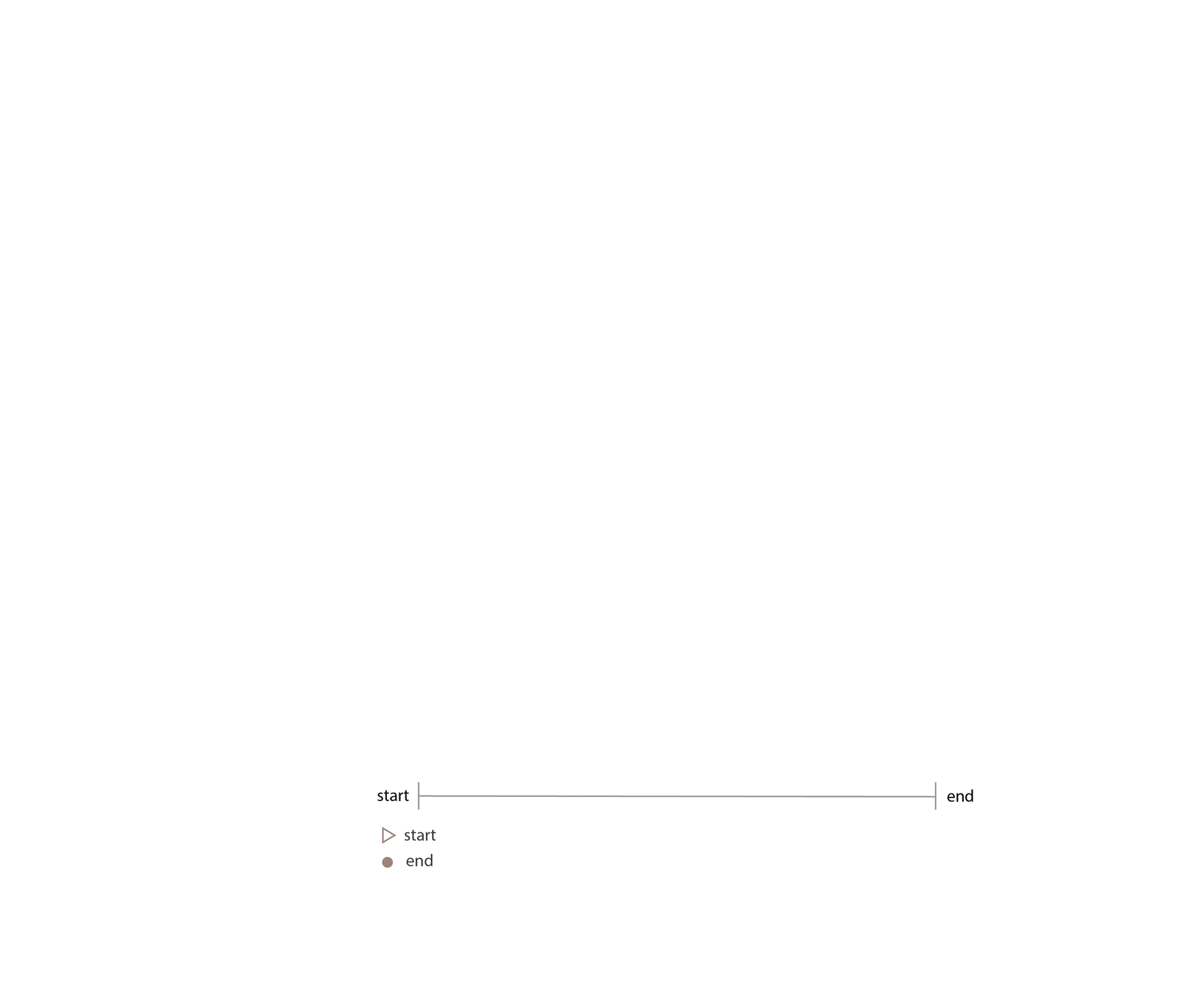
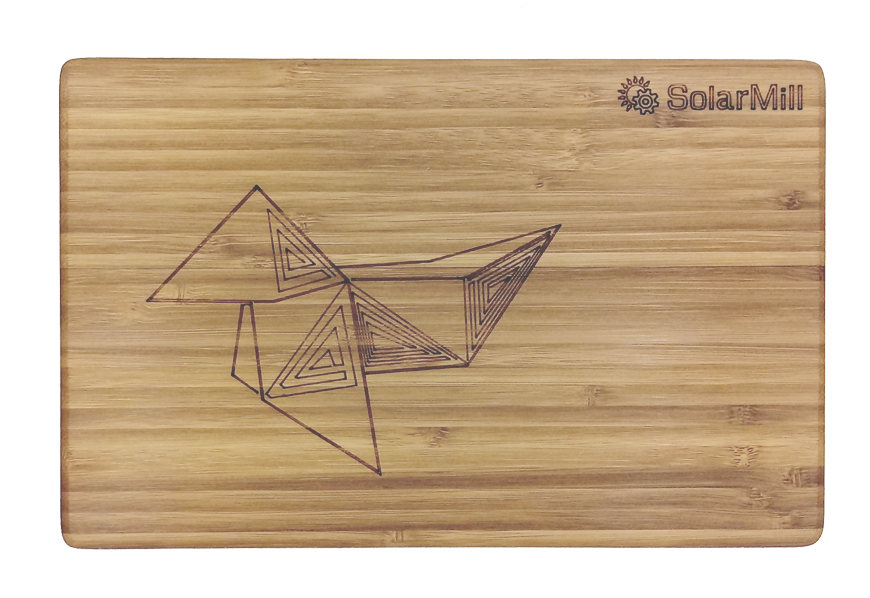
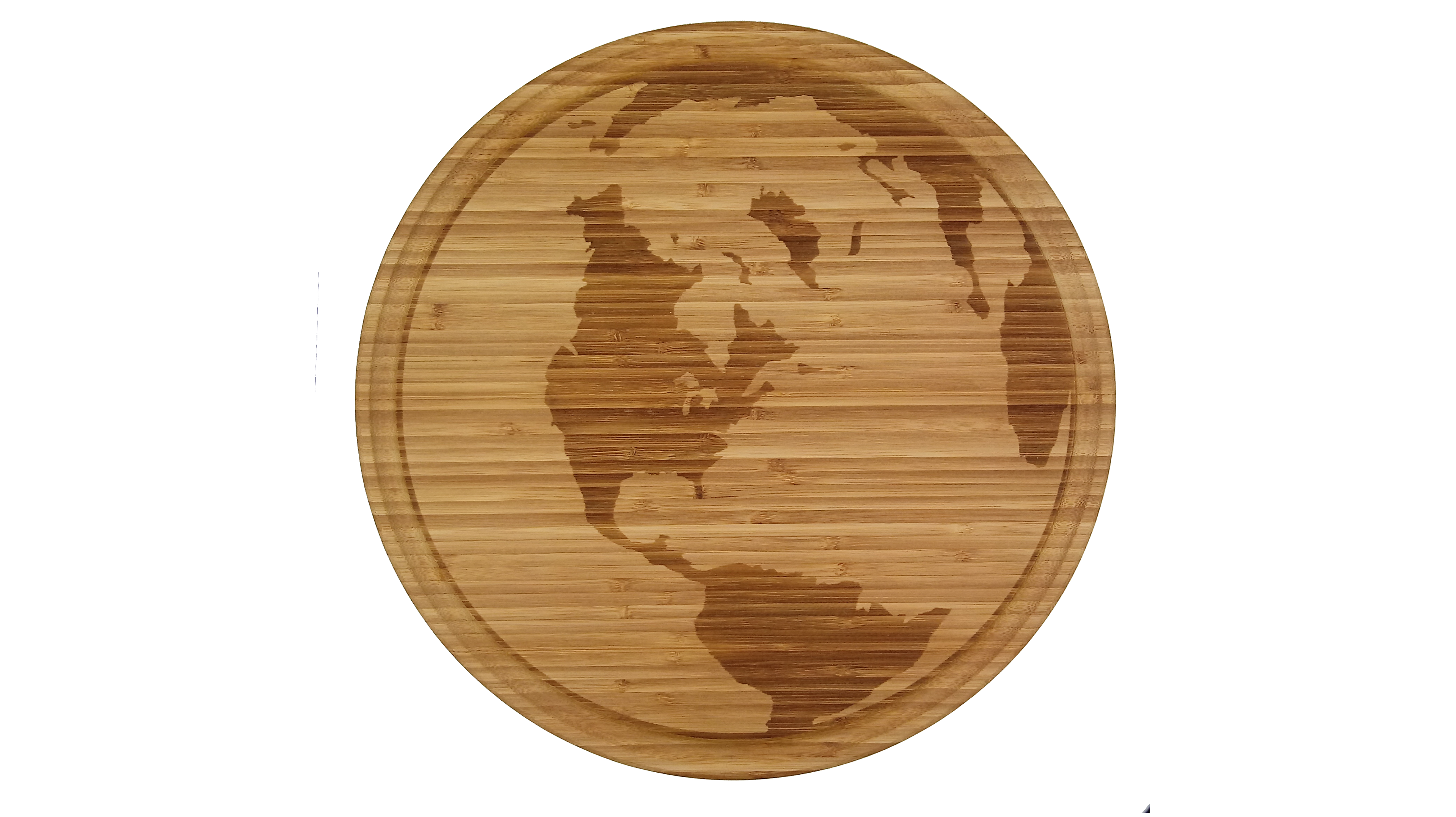
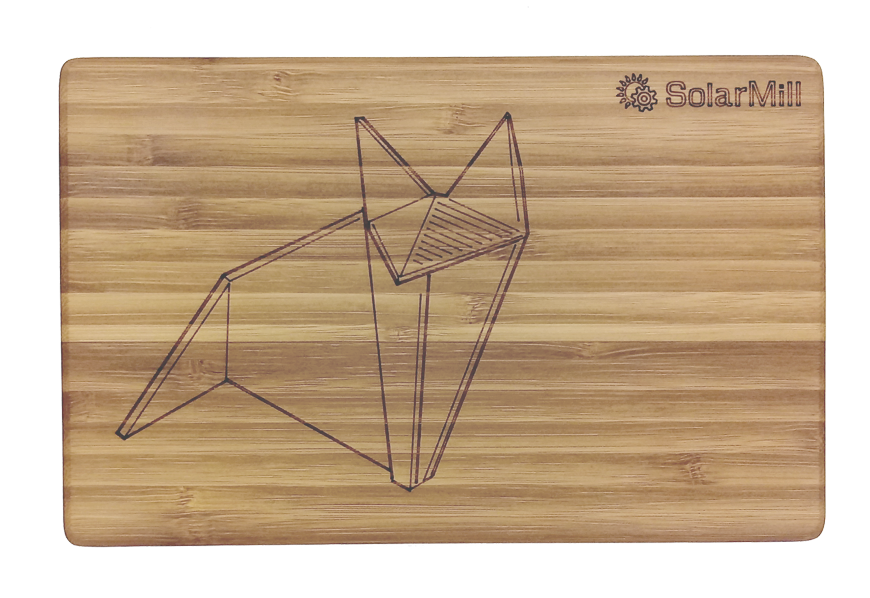
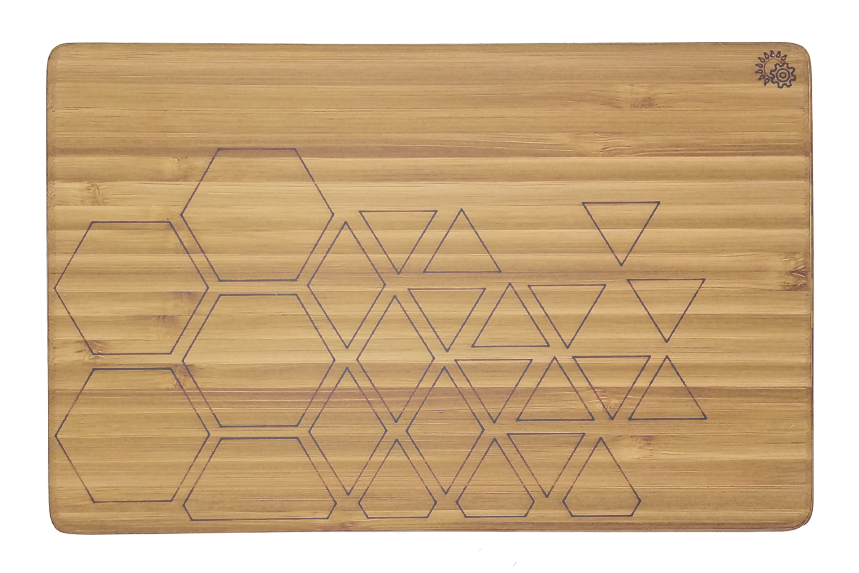
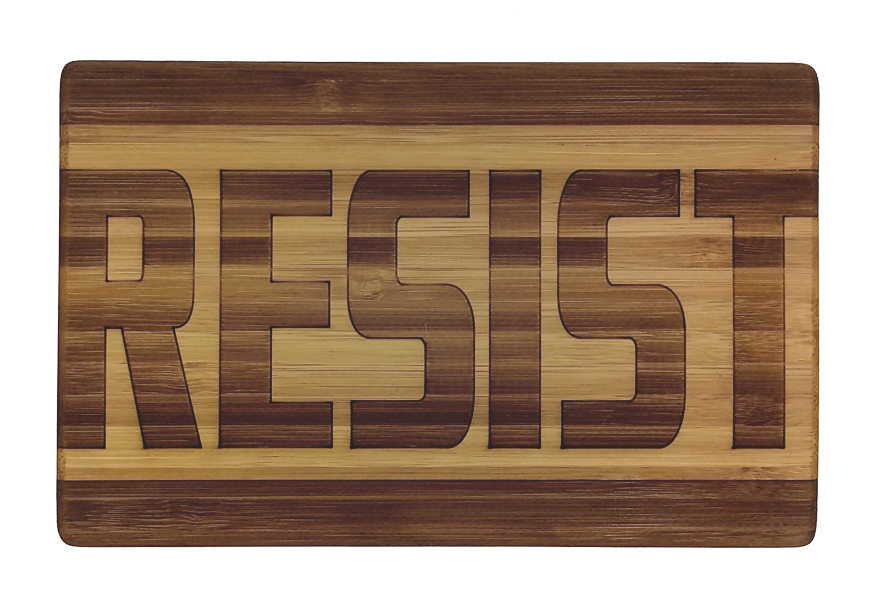
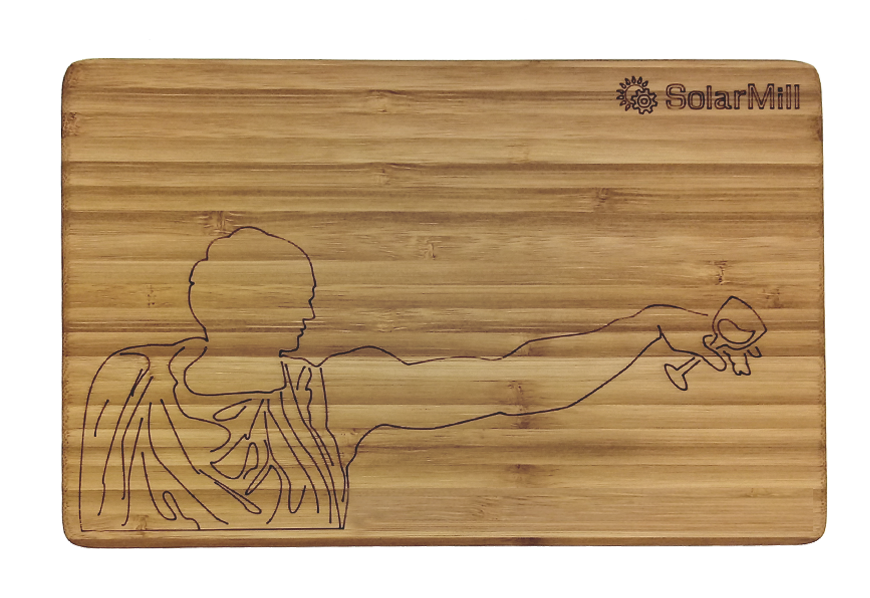
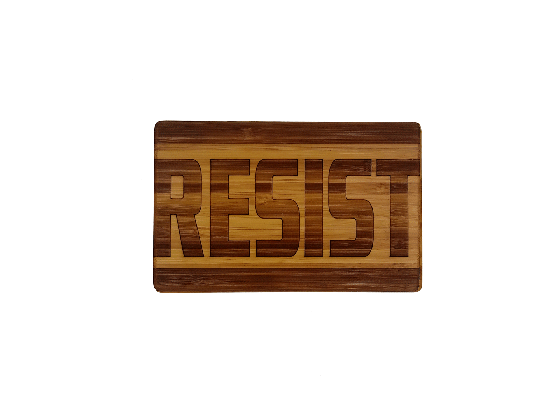